At present, efforts to address environmental issues have become a common recognition throughout the world.
In particular, we believe that efforts to reduce CO2 emissions, which are said to be the cause of global warming, are our responsibility to live today in order to leave the beautiful earth to the next generation.
And we also believe that using our proprietary surface treatment, such as NANOTECT® and TAKECOAT®-1000, for steel products(nuts and bolts. Etc.) at customers' Oil・Gas・Marine plants will contribute to reducing CO2 emissions (zero emission) in our customers' LCA(Life Cycle Assessment).
Life Cycle Assessment (LCA) is a method to quantitatively evaluate the input resources and environmental load of these resources and the potential environmental impact on the earth and ecosystems during the life cycle from the procurement of raw materials for products, production, distribution, consumption, maintenance, disposal and recycling.
-
procurement of raw materials -
production -
distribution -
consumption, maintenance -
disposal, recycling
Non-coated Bolt (replacement in once a year)
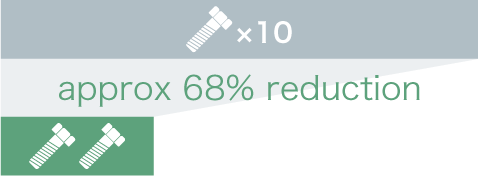
NANOTECT® or TAKECOAT®-1000 (replacement in every 5 years)
By using NANOTECT® or TAKECOAT® -1000,CO2 emissions throughout the entire life cycle are greatly reduced life cycle are greatly reduced by extending the life of steel materials.
In this way, please use our Takenaka products as a powerful means of demonstrating the long-term soundness and environmental awareness of your important plants in and out of the country.
Takenaka’s Approach To Environmental Measures
Reduction of CO2 emissions
by reducing consumption
CLICK
CLOSE
1Viewpoint from rust prevention performance
CO2 emissions(tons) associated with the production and replacement of steel products are given CO2 emissions=emission factorx annual consumption(tons) x number of products replaced
(remark:number of replacement includes the first installment)
Assuming the customer’s equipment life is 10 years, the emission factor is 【2.0】*1, and the annual consumption of steel material is 300tons*2 , CO2 emissions over 10 years should be as follows :
In case of Non-coated Metal, Rust prevention function maintenance life is 1 year*3☛replacement in every year
CO2emissions = 300tons x 10times replacement = 6,000tons
In case of usual PTFE coated metal, Rust prevention function maintenance life is 2.5years*3☛replacement in every 2.5years
CO2emissions = 2.0 X 300tons X 4times replacement = 2,400tons
In case of NANOTECT® and TAKECOAT®-1000, Rust prevention function maintenance life is 5years*3 ☛replacement in every 5years
CO2emissions = 2.0 X 300tons X Twice replacement = 1,200tons
- *1:CO2 emissions per unit of production (quoted from data from the Ministry of the Environment
- *2:Our own trial calculate,
- *3:Calculated independently from the correlation between corrosion test data and actual environment exposure test at our company and public third party organizations
For reference;
Extending the life of steel products not only reduces CO2 emissions, but also reduces the cost of products by reducing the number of replacements. In addition, cost reductions such as [personnel expenses due to replacement] and [losses due to equipment stoppages] must also be considered.
In other words, extending the life of steel products not only reduces CO2 emissions, but also has a significant impact on LCC (Life Cycle Cost).
According to our estimates, approx.80% cost reduction will be achieved in 10 years by using NANOTECT® and TAKECOAT®-1000. The advantages of NANOTECT ® and TAKECOAT®-1000 are obvious.
LCC = P1 + Nreplace (P1 + Creplace + Cstop + Cfailure)
Nreplace = (Set life of equipment/Performance life of bolt) – 1
P1 = Unit price of Nut&Bolt
Creplace = Labor cost at maintenance
Cstop = Expenses for equipment shutdown
Cfailure = Cost of equipment shutdown by corrosion
2 Viewpoint from Transportation
Our products are used not only in Japan but also in overseas, so we would like to explain CO2 emissions from both overseas transportation (marine) and local transportation (truck).
CO2 emissions (ton) in transportation is shown
CO2 emissions = emission intensity(g-CO2/ton・km)*4 X weight of part (ton) X transportation distance (km)
CO2 emissions over 10 years assuming a customer's equipment life is 10 years and the weight of parts to be replaced are 300 tons should
be as follows:
In case of Non-coated metal :
Marine *5 CO2 emissions = 10 times transportation x 39 x 300ton x 7,000km = 819ton
Truck *6 CO2 emissions = 10 times transportation x 173 x 300ton x 500km = 260ton
In case of usual PTFE coated metal;
Marine *5 CO2 emissions = 4 times transportation x 39 x 300ton x 7,000km = 328ton
Truck *6 CO2 emissions = 4 times transportation x 173 x 300ton x 500km = 104ton
In case of NANOTECT® and TAKECOAT®-1000 coated metal ;
Marine *5 CO2 emissions = 2 times transportation x 39 x 300ton x 7,000km = 164ton
Truck *6 CO2 emissions = 2 times transportation x 173 x 300ton x 500km = 52ton
*4: CO2 emissions intensity in transportation methods (based on data from the Ministry of Economy, Trade and Industry In case of Marine:39, in case of Truck;173
*5: Marine transportation from Japan to UAE[distance approx.7,000km]
*6: Land transportation from Osaka to Tokyo[distance approx.500km]
In case of Japan → UAE by marine : 7,000Km, in case of Osaka → Tokyo by truck ; 500km
Reduction of CO2 emissions
through improvement of facilities
CLICK
CLOSE
☆1Improvement of Coating Equipment
In most cases, heating and curing of polymer coating films is required for the formation of high-performance coatings for rust resistance.
Takenaka is also focusing on environmental measures for its production facilities, and has implemented improvements to coating film curing facilities to generate coating film during curing. CO2 emissions have been curbed.
★CO2 emissions before improvement
When surface treated with 300 tons of steel per year with conventional equipment, 501 tons of CO2 were emitted annually.
★CO2 emissions after improvement
By changing the heat source and effectively utilizing the waste heat generated during curing in the heating and curing equipment, CO2 emissions have been reduced to 400 tons per year. Namely, we have reduced CO2 emissions by 100 tons per year. This is a 20% reduction compared to the previous model.
☆2Polymer Coating Method
Takenaka's annual paint consumption is 10 tons. Since the CO2 emissions coefficient in paint production is 0.6 / 10 tons*7,
In general PTFE, it is replaced once every 2.5 years = 2.4 tons/CO2 emissions per 10 years
On the other hand, regarding NANOTECT ® and TAKECOAT ® - 1000, our annual CO2 emissions are 0.6 tons. Since it is replaced once
every five years, it = 1.2 tons/10 years of CO2 emissions.
*7: Data from the Ministry of Economy, Trade and Industry and the Japan Paint Manufacturers Association
Summary of Takenaka‘s Original Environmental Measures
Takenaka's surface treatments "TAKECOAT®-1000" and "NANOTECT ®" reduce CO2 emissions by approximately 68% over 10 years of use、 compared to the Non-coated steel products.
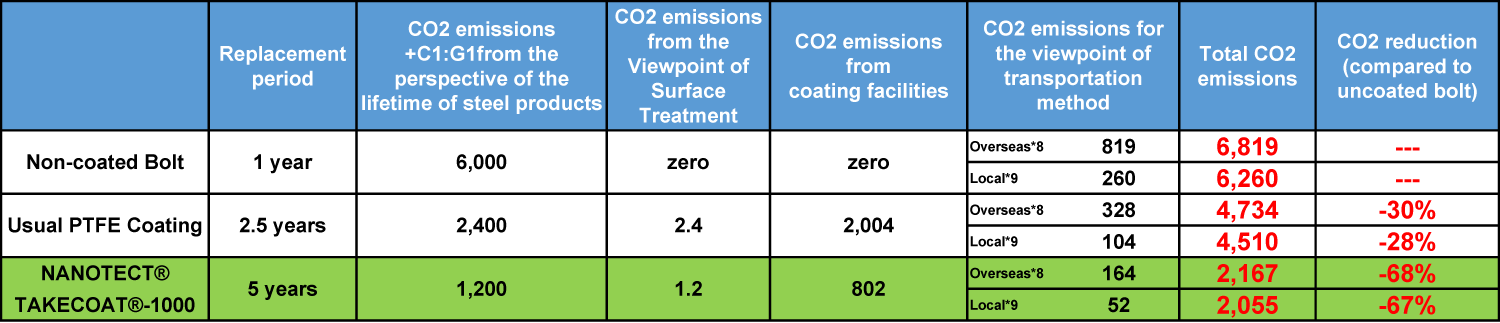
*8:Marine transportation from Japan to UAE[distance approx.7,000km] *9:Land transportation from Osaka to Tokyo[distance approx.500km] Unit:tons
※The table can be slid sideways.

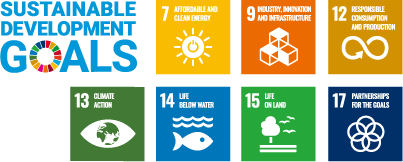
Takenaka Seisakusho Co,,Ltd and TAKENAKA MIDDLE EAST LLC support the Sustainable Development Goals (SDGs)
In this way, by using these environmentally friendly Takenaka products, we believe that we can help customers make their wonderful factory facilities maintenance-free and declare that they are more environmentally friendly systems both domestically and internationally.
Please consider Takenaka products in your lineup of environmental conservation and equipment maintenance.